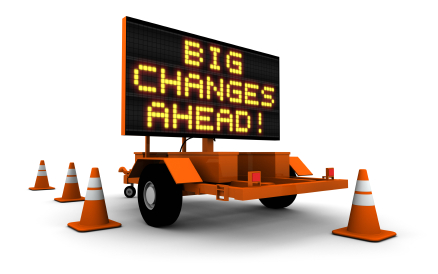
New changes to the Occupational Safety and Health Administration’s (OSHA) Hazard Communication Standard are bringing the United States into alignment with the Globally Harmonized System of Classification and Labeling of Chemicals (GHS), further improving safety and health protections for America’s workers. Building on the success of OSHA’s current Hazard Communication Standard, the GHS is expected to prevent injuries and illnesses, save lives and improve trade conditions for chemical manufacturers. The Hazard Communication Standard in 1983 gave the workers the ‘right to know,’ but the new Globally Harmonized System gives workers the ‘right to understand.
Hazard classification: Provides specific criteria for classification of health and physical hazards, as well as classification of mixtures.
Labels: Chemical manufacturers and importers will be required to provide a label that includes a harmonized signal word, pictogram, and hazard statement for each hazard class and category. Precautionary statements must also be provided.
Safety Data Sheets: Will now have a specified 16-section format.
Information and training: Employers are required to train workers by December 1, 2013 on the new labels elements and safety data sheets format to facilitate recognition and understanding.
via Hazard Communication.